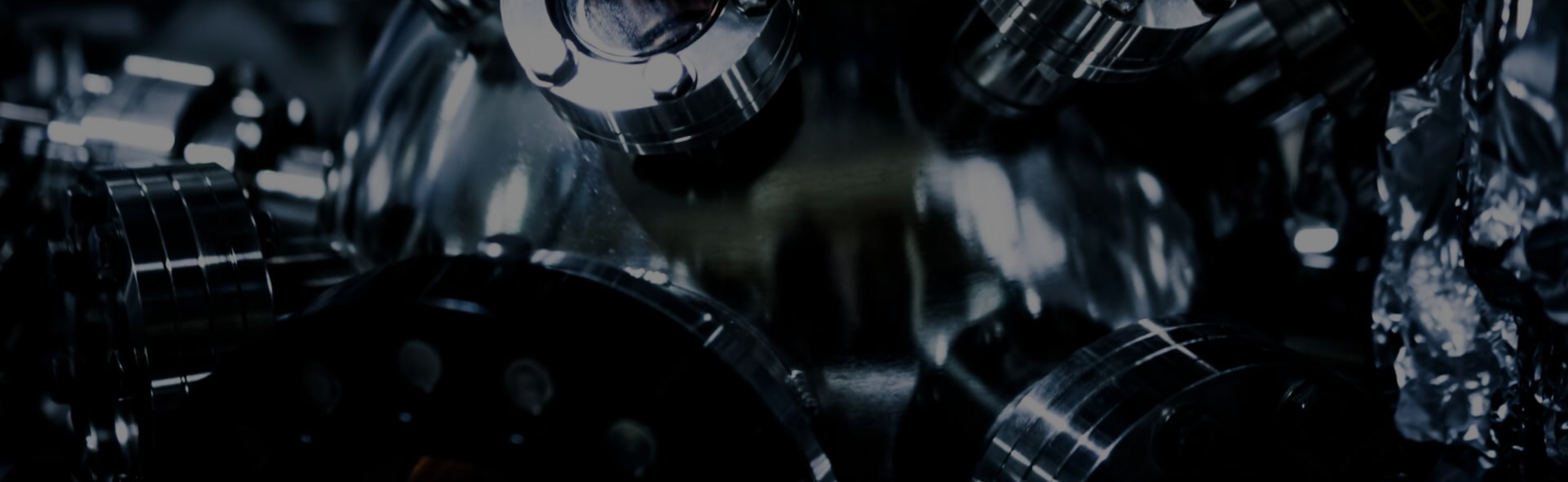
技術コラム
IoTを製造工場に導入すると?生産改善点を見える化した事例をご紹介します!
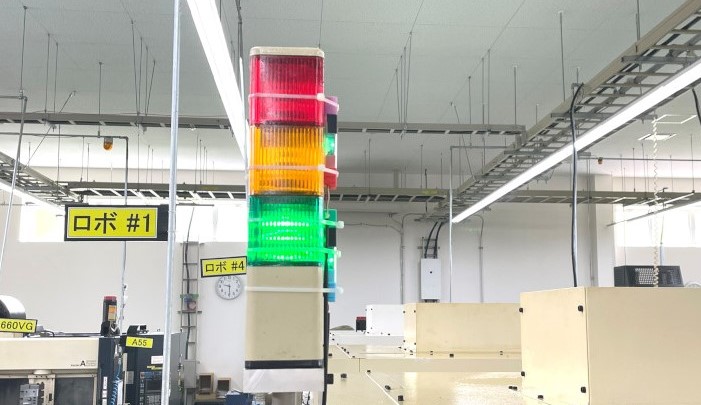
発行日:2024年6月26日
IoTを利用した稼働情報収集システム活用の紹介
佐渡精密では2021年にIoT(Internet of Things)を利用した加工機の稼働情報収集システムを開発しました。運用開始から3年ほど経ちますが、今では工場のほとんどの加工機に搭載され、進化を重ね、様々な分析が可能となりました。
その活用事例と開発までの道のりをご紹介致します。
稼働情報収集システムでできること
・リアルタイムでの加工機の状態把握 ⇒『設備状況マップ』
・加工機毎の稼働情報集計、分析 ⇒『設備状況チャート』
実はできる事はこの2つだけですが、収集したデータの使い方次第で無限の活用方法があります。
活用方法をご紹介
『設備状況マップ』
どこにいてもリアルタイムで加工機の状況を把握することが可能です。
マシニング加工などは、加工終了後に製品の回収と材料の供給作業が必要となるため、加工終了から次の加工を開始するまでの時間を短くすることは、稼働率を上げることに繋がります。状況マップをスマホやタブレットに表示させて持ち歩けば、効率の良い材料供給が可能になります。さらに加工終了時間を自動予測するカウントダウンタイマー機能も搭載しているので、次にどの機械が何分後に終了するかが分かるようになり、更なる効率化につながっています。
『設備状況チャート』
加工機械別,加工期間別,昼夜別など、データの比較分析から課題が浮き彫りになり、
その改善効果もデータで確認ができるため、「工場の見える化」=「課題の見える化」=「改善効果の見える化」が可能になりました。
例えばこのシステムを導入する以前は、“生産性を上げる為には加工時間の短縮こそが有効な手段である“と考えていましたが、加工時間を短縮してもなかなか1日当たりの加工数が伸びず、「なぜだろう?」と悩んでいました。
しかしシステム導入後にデータを見てみると、加工時間は毎回同じ時間なのに対し、待機時間はバラツキが非常に大きかったのです。実際に加工データを収集することによって、“待機時間を短縮、安定化させることの方が生産性UPにつながる”という事がわかりました。
自社開発の強みを最大限に!!
システムが自社開発の為、現場からの【こんなデータを表示したい】や【こんな機能を追加してほしい】などのリクエストに即対応でき、日々進化しています。
開発までの道のり
実は当初、加工機の稼働情報収集システムを自社開発するつもりはありませんでした。世の中には既にこのような事ができる完成されたパッケージシステム品が沢山あるため、「私たちがやりたい事に合致するのはどれか」、「コスト的にはどれがお得か」などの指標で選定をしているところでした。
しかしどれも痒い所に手が届かない感じで、やりたい事が微妙にできなかったり、機能の後付けが難しかったりでもどかしく、しかもどれも非常に高価な物でした。
いろいろ情報収集している中で、システムの自作に関する情報も自然と入ってきていました。その内容を見てみると、次第に《これなら何とか自分たちで作れるのではないか》と考え始めました。
それはとてもシンプルな物で、加工機についている既存の積層表示灯に『光センサ』を取付け、どのランプが点灯しているかを『シングルボードコンピューター』に信号として取り込み、簡単なプログラムでデータを収集/蓄積してシステムを構築するというものです。
また何よりも魅力的だったのが、パッケージシステム品に比べ非常に安価にできる事でした。
こうして得た方法を元に、独自に『スライドスイッチ』を2つ追加し、弊社のシステムの運用が始まりました。最初は十数台の加工機に設置して小規模での運用を開始しましたが、3年が経過した今では工場内のほぼすべての加工機に設置され、約100台の加工機の状況をデータ収集しています。
上:安価な光センサとエンドミルケースでセンサパッケージを作製
下:コンピューターのケースは食品保存容器を利用
手作りのスライドスイッチ
まとめ
〇生産性及び機械の稼働率を上げるためには、加工時間の短縮のほか、待機時間の短縮も有効である。
〇完成されたパッケージシステム品は世にたくさん出ているが、求めている内容に合致するものを探し出すのに時間が掛かる場合や、導入予算に見合わない場合がある。
〇システムを自社開発することで、現場が求めている機能をピンポイントにつくることが出来、修正や要望もすぐに反映させることが出来る。