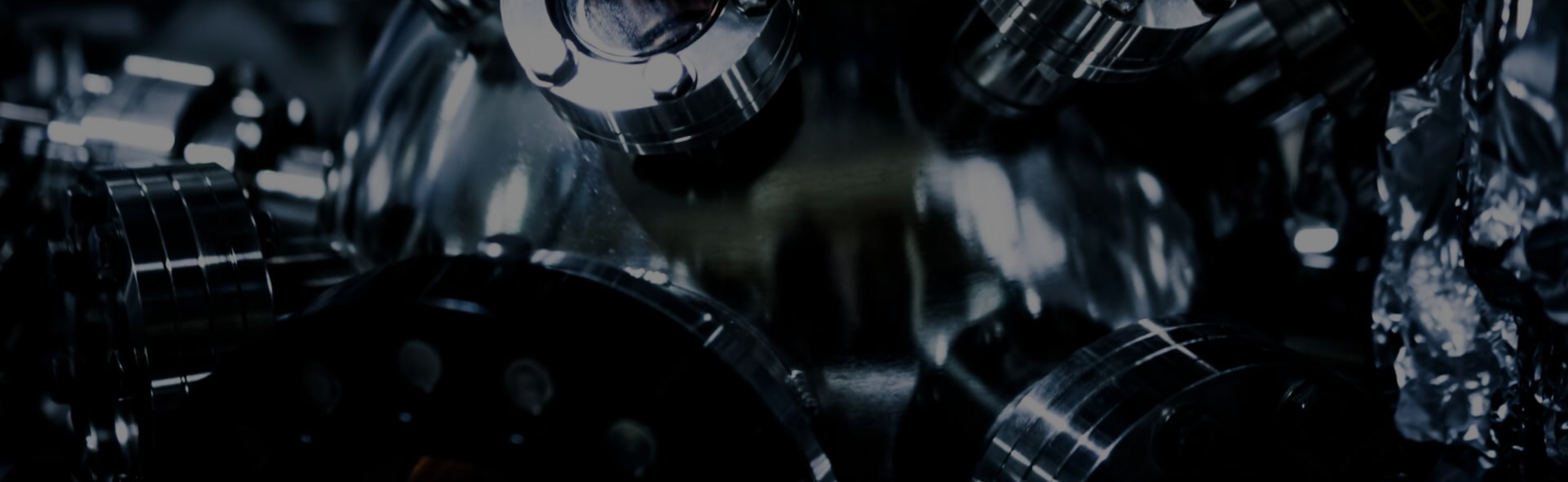
技術コラム
【例題あり】工作機械の主軸特性とは?ポイントを図表で解説!
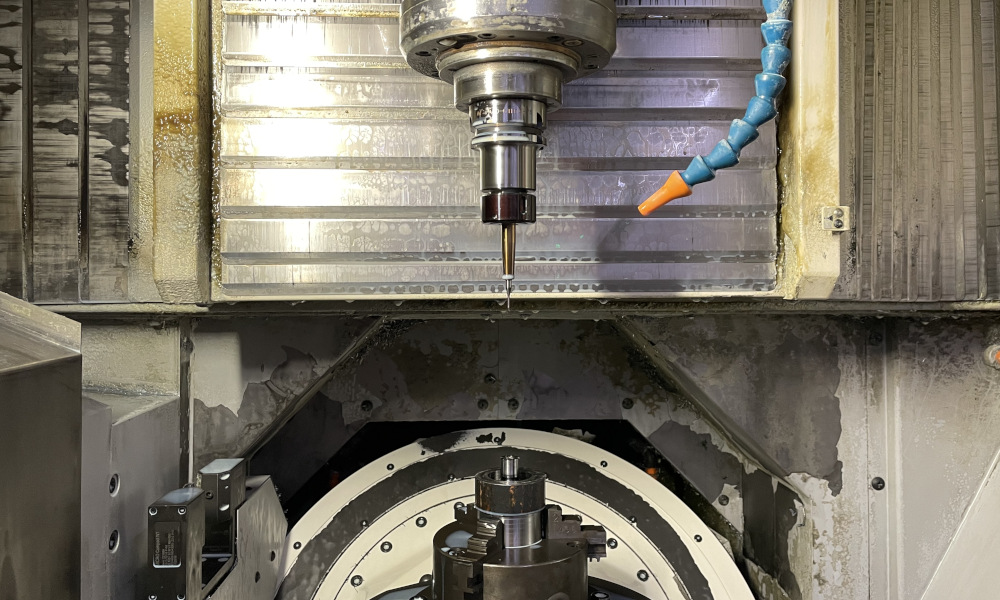
発行日:2024年5月24日
機械の主軸性能
工作機械における主軸性能は、工具選定や切削条件の最適化に重要となる要素です。
切削負荷が大きい加工で主軸に負荷がかかり機械が停止したり、逆に性能を活かしきれていないまま非効率な切削条件で加工してしまっているケースが存在します。
機械ごとの主軸性能を理解すれば、より効率の良い加工を行うことができます。
出力とトルク
主軸性能を考える上で「出力」「トルク」という言葉が重要になります。
出力
◎出力 = 材料を一定時間内にどれだけ削れるかを表す能力
出力は仕事率とも云われ、「単位時間当たりにどれだけ仕事ができるか」を表します。
自転車でいえばペダルを速く漕げる能力、主軸性能でいえば、材料を沢山削れる能力です。
加工において下記の関係があり、Qは1分当たりの材料除去量(切削体積)です。
※定数Cは、加工方法によって数値が異なります。
出力P[kW]=切り屑排出量 Q[cm³/min]×定数C |
よって、高出力を出せる機械で高出力で材料を削れば、一定時間内でより沢山削れる、即ち能率の良い仕事ができることになります。勿論、切削条件を上げる際に工具欠損や振動を起こさないことが前提です。
トルク
◎トルク = 主軸を回転させるために必要な力
トルクは簡単に言えば、「ものを回転させる力」のことです。
自転車のペダルを漕ぎ出す際のように、主軸も回し始めが最もトルクを必要とします。
大きいトルクを出せれば加速が良く、高速回転の状態に速く到達できます。
加工において下記の関係があり、工具が大径になれば、切削に必要なトルクも大きくなります。
トルクT[Nm]=(切削抵抗F[N]×工具半径 r[m]) |
主軸の保有するトルクが大きいほど、より負荷の大きい仕事をすることができます。
トルク値の大きさは主軸剛性の指標です。
出力とトルクの関係性
P≒TS/9549 出力:P[kW] トルク:T[Nm] 回転数:S[rpm] |
式から、出力Pは回転数Sに比例、トルクTは回転数Sに反比例します。
つまり、回転数が上がると出力が一定の場合、トルクが下がってきます。自転車の例だと、回転が速くなりスピード(=出力)が出てくると、ペダルを漕ぐ力(=トルク)がそれほどかからなくなる感じです。
引用:切削加工の専門書と論文のリストとオススメ
「トルクの計算方法による影響」
(https://cuttingbooklist.sarashi.com/torque_calculation.html)
主軸の出力・トルクがより重要となる場面
出力が重要
・非鉄金属の高能率加工
・小径エンドミルでの高速加工
主軸負荷は比較的少ないため、高出力で材料を素早く除去できることが重要です。
トルクが重要
・難削材の加工
・大径工具での重切削加工
・タップ・ボーリング加工
一般的に低回転で加工するため、高トルクを有する(≒パワフルな)機械が有利です。
主軸性能を考慮して加工に適した工作機を選定する
下記の表は、弊社保有の幾つかの加工機の主軸特性をまとめたものです。(仕様書参考)
なお、相対的に出力とトルクが高いものを濃い色、低いものを薄い色で示しました。
例えば、Aは高トルクを有し重切削加工により向いています。
また、Dはトルクは低めですが、出力が高めで高速加工により向いています。
〇低回転主軸の大型機は高トルクのものが多く、難削材の加工や重切削に向きます。
〇高回転主軸になると、出力が大きい反面トルクが低いものが多いです。
※一般的な加工では、概ねどの機械でも十分な出力・トルクを有しています。
機械の主軸性能のまとめ
〇機械主軸の性能は、工具選定や切削条件を決める際に重要となる一要素です。
〇主軸性能を考える上で、「出力」「トルク」の大きさが重要になります。
〇加工分野において、「出力」は一定時間内にどれだけ材料を切削できるかを表す能力値、「トルク」は主軸を回転させるために必要なパワーです。
〇出力が高いほど能率の良い加工ができ、トルクが高いほどパワフルな加工ができます。
〇非鉄金属をザクザク削りたいときは高出力機で高回転領域を使い、切削負荷のかかる加工は高トルク機で低回転領域を使うと良いでしょう。
主軸性能の具体例
前半では、切削加工では機械主軸の性能が重要な要素となると記載しました。
ここからはグラフや式を交えながら、具体的に主軸性能を考慮して加工条件が適切そうか判断していく方法を述べていきたいと思います。
主軸特性図について
工作機械の仕様書には、主軸ごとの性能(=主軸特性)についてグラフに表したものが記載されています。これが「主軸特性図」です(トルク線図・出力線図等ともいう)。具体的には主軸回転数と出力値・トルク値と呼ばれる数値の関係を示したものです。
横軸:主軸回転数
縦軸:出力値・トルク値
参考:モノタロウ「マシニングセンタの基礎講座 5-1主軸の性能(基底回転数)」
(https://www.monotaro.com/note/readingseries/machiningcenterkiso/0501/)
〇出力は回転数が高くなると上昇し、一定の回転数(=基底回転数)に達すると安定します。
〇トルクは回転数が基底回転数未満で安定し、それを超えると徐々に減少します。
佐渡精密、MCの例
主軸特性図の例(弊社保有のマシニングセンターの特性図を抜粋)
出力・トルクの表記
〇上記の加工機の場合、30分なら22kW、連続運転なら18.5kWの出力で使用でき、15分で151Nm、連続運転なら124Nmのトルクで使用できます。
定格出力:18.5kW
定格トルク:124Nm
※ トルク特性のグラフ内で「25%EDトルク 239Nm」と表記があります。
ED「負荷時間率」=100(t₁/t₀) t₁=運転時間 t₀=運転時間+停止時間(1サイクル) |
25%EDであれば、1サイクル4分の場合、1分だけ運転する状態を示します。
※グラフによってはトルクの単位記載が異なります。 1kgfm=9.8Nmです。
切削条件と出力トルクに関する注意点
切削条件を設定する際、
〇連続運転が可能な出力未満になるよう考慮します。
〇連続運転が可能な負荷トルク未満になるように考慮します。
これを超えて運転すると、機械に負荷がかかり主軸が停止してしまうことがあります。
フライス加工における出力・トルクの計算
所要動力 Pc[kW] (径方向切込み量ae ×軸方向切込み量ap ×切削抵抗 F ×比切削抵抗kc) = (60×10⁶×η) |
所要トルク Mc[Nm] (径方向切込み量ae ×軸方向切込み量ap ×1回転当たりの送り ×比切削抵抗kc) = (2π×10³) |
※上記解説の式では単位を省略していますが、後述の例題にて記載しています。
※比切削抵抗kc:単位切削面積[m²]当たりの切削抵抗
→小さいほど「削りやすい」。
参考:住友電工ハードメタル
※企業や掲載サイトによって、値は多少異なります。
切削タップの出力・トルク計算
◎所要動力Pc[kW]=0.000104N×Tc |
→実際は種々の損失等を考慮すると、計算値の4倍程度必要になります。
◎所要トルクTc[Nm]=(tanθ/24000)kc・K(D-Do)²(D+2Do) θ:ねじ山の半角 K:補正定数 D:タップ外径 Do=下穴径 kc:比切削抵抗 |
→タップ径が大きいほどトルクがかかります。
参考:OSG 加工相談FAQ「一般タップ仕様 タップ加工トルク」
(https://faq.osg.co.jp/faq/show/492?category_id=43&site_domain=default)
★転造タップの場合、塑性変形のため、さらにトルクがかかります。
事例 スパイラルタップで加工する際に必要なトルク
(被削材S45C、メートル並目ネジ)
右側の表を見ると、タップ径が大きいほど、所要トルクも増えているのが分かります。
例題 出力・トルクの観点から見て加工可能かを検討する方法
アルミ合金をマシニングセンタ-にて、以下の条件で切削する場合(※数値は例)、出力・トルクの観点から切削が可能か検討してください。
主軸特性図は先ほど例に示した2つのグラフを使用してください。
〇使用工具:φ16エンドミル(3枚刃)
〇回転数S:12000[rpm]
〇XY切込量ae:16[mm]
〇Z切込量ap:16[mm]
〇切削送り速度F:3000[mm/min]
〇1回転当たりの送り量fn:0.25[mm/rev]
〇アルミ合金の比切削抵抗kc:800[MPa]
〇機械効率η:0.8
A.所要動力Pc=(ae×ap×F×kc)/(60×10⁶×η)=12.8kW
S=12000領域でこの加工機の定格出力は18.5kWなので、加工可能とする。
A.所要トルクMc[Nm]=(ae×ap×fn×kc)×(2π×10³)≒8.15Nm
S=12000領域でこの加工機の定格トルクは14Nm程度なので、切削可能とする。
結論としては、出力・トルク両観点から見て切削は可能と分かります。
しかし、あくまで理論上の数値なので実際の加工では余裕をもって条件を設定しましょう。
主軸性能の具体例のまとめ
〇高い出力・トルクを要する加工では、機械の主軸特性図のグラフを参考にして、計算値がグラフに描かれた線よりも下にあることを確認しましょう。
〇出力やトルク値は回転数以外にも、工具径や切込量・材質等にも影響を受けます。また、転削や旋削・ドリル等で計算方法も変わるので、計算式の載っているサイトを参考にしましょう。
〇特にM10以上のタップやφ16以上のエンドミルを使う際は、負荷に注意しましょう。