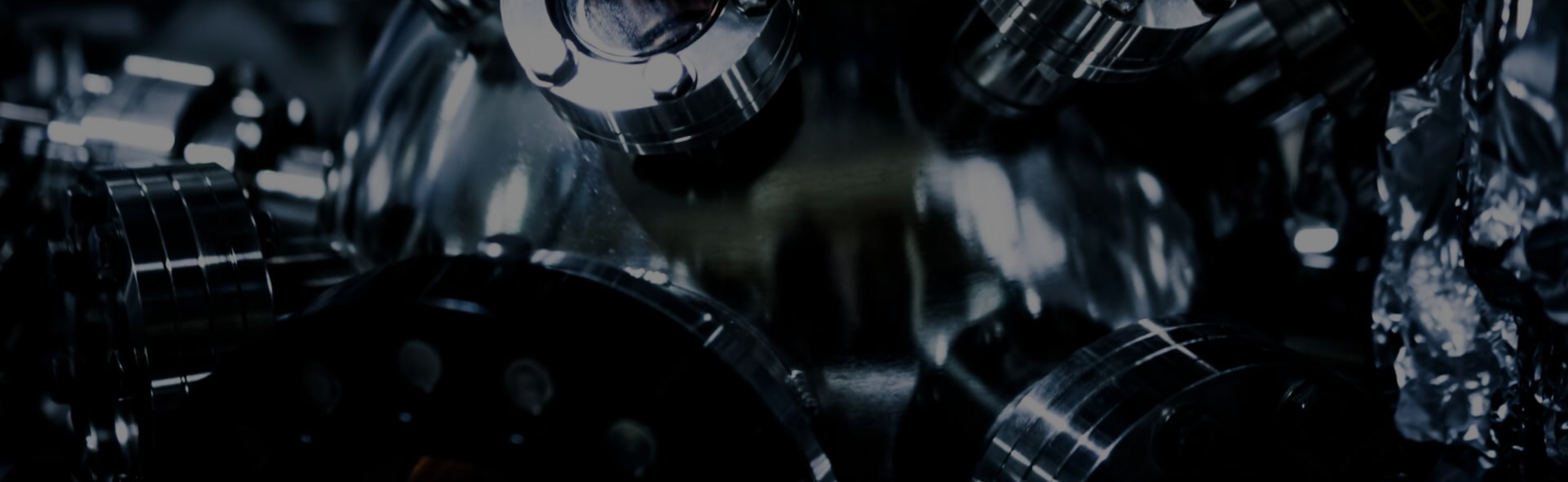
技術コラム
ハードミーリングとは?用途やポイントについて解説!
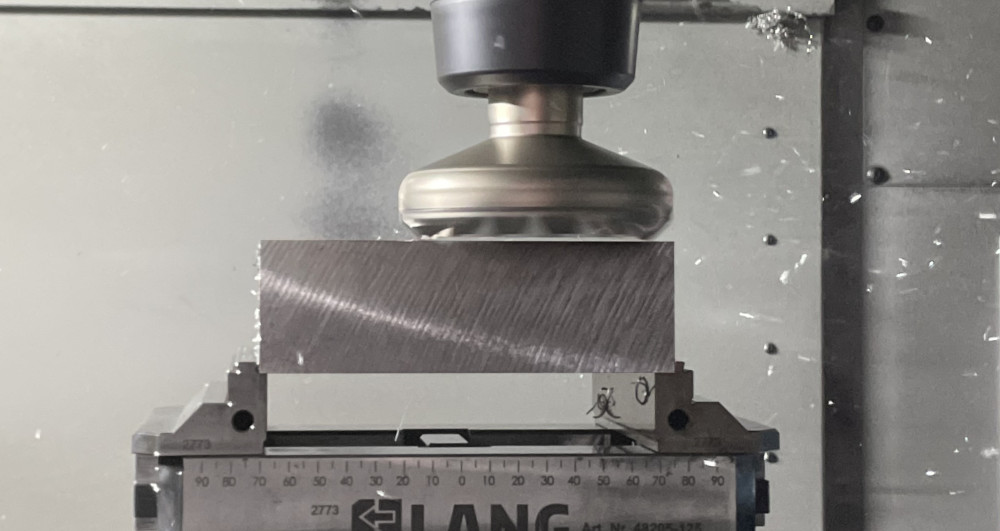
発行日:2025年4月24日
金型部品や高硬度材の加工といえば、これまでは研削加工が常識とされてきました。しかし近年、焼入れ鋼を直接切削する「ハードミーリング」が注目を集めています。
工程短縮、コスト削減、さらには加工精度の向上まで可能にするこの技術。今回は、ハードミーリングの基礎から実際の活用ポイントまでをご紹介します。
ハードミーリングとは?
ハードミーリングとは、一般的にHRC50以上の高硬度材(焼入れ鋼など)を、超硬エンドミルなどを用いて直接フライス加工する技術のことを指します。
従来、焼入れ後のワークは研削加工で仕上げるのが一般的でしたが、近年の工具技術や機械性能の進化により、切削でも十分な精度が得られるようになりました。
ハードミーリングのメリットとデメリット
メリット
・工程・納期の短縮
焼入れ前の荒加工 → 焼入れ → 研削 という流れを、焼入れ後のハードミーリングだけで完結できる場合もあり、研削工程を省くことで、リードタイムを短縮することが可能です。
・コストダウン
研削を外注している場合は外注工程の削減や、自社内加工の範囲拡大を見込めます。
・自由度の高い形状加工
研削では難しい複雑な形状も、マシニング加工であれば柔軟に対応することが出来ます。
デメリット
・工具コストが高くなる(特にCBN)
・加工条件の最適化にはノウハウが必要
・工作機械側の剛性・精度が求められる
ハードミーリングが向いている加工・向いていない加工
◎向いている
・小物金型部品の仕上げ(パンチ・ダイ・キャビティ部など)
・ポケット形状や3D曲面
・研削では加工が難しい複雑形状や微細形状
×向いていない
・平面・真円などの高精度仕上げ
・超硬やセラミックなどの切削が難しい材質
加工のポイント
高硬度材を切削するには、適した工具や機械の選定が不可欠です。
工具の選定
耐熱性や耐摩耗性の高いものを選ぶことが重要です。またコーティングによってクーラントの必要性が異なるため、メーカーの推奨条件を確認した上で選定してください。
・材質:超硬工具(ナノ粒子系が特に有効)、CBN工具(立方晶窒化ホウ素)など
・コーティング:TiAlN系(窒化アルミニウム)、AlCr系(アルミニウム・クロム)、PVDコーティングなど
クーラント(切削油)の使用
ハードミーリングは、硬度が上がるにつれて加工時の温度も高くなります。
通常、クーラントは切削時に発生する熱を冷却したり、工具とワークの摩擦を減少させることによって「工具寿命の延長」や「寸法安定性の向上」、「切り屑の排出」などのメリットがありますが、ハードミーリングにおいては熱変動や熱衝撃などのデメリットもあります。
・ドライ加工が一般的だが、加工条件によってはウェット加工やミスト加工を使い分ける必要がある
・非常に高温になるため、クーラントによる急激な冷却で工具に熱衝撃(サーマルショック)が加わり、欠けや割れの原因となる
・冷却と加熱の繰り返しによる寸法変動により寸法変化が不安定になる場合がある
・超硬工具や、セラミック工具は特に注意が必要
加工機の剛性と主軸性能
工具への負荷が高いため、高い主軸剛性・熱変位・振動対策がされたマシニングセンタが求められます。
・切削時のビビリを防ぐ高剛性構造が重要
・工具の突出し長さを短くし、たわみを抑え共振を防ぐ
・共振を防ぐため、不等リード・不等ピッチのエンドミルを使用する
・ホルダーを高剛性なものに変更
・加工機のベースや工作物の固定、アンカー設置などにより共振を防ぐ
切削条件の最適化
ワークの硬度や摩擦によるビビリの抑制、加工面の精度を保つため、最適な加工パスや適正な切削条件を設定することが重要です。工具へ掛かる負荷を均一にすることで、破損を防ぎ工具寿命を延ばすことが可能です。
・切粉を分断し、加工による熱を逃がす
・小切込み・高送りのトロコイド加工などを活用し、一度にかかる負荷を分散する
・加工熱をコントロールするパス設計
・荒加工と仕上げ加工を分ける
よくある課題とその対策
まとめ
・ハードミーリングはHRC50以上の焼入れ鋼を切削できる技術です。
・メリットとしては、工程短縮・コスト削減・加工形状の自由度が挙げられます。
・工具やコーティングの選定、加工条件の最適化などが重要となります。
・ドライ加工が一般的ですが、加工条件等によってはウェット加工やミスト加工を使い分ける必要があります。
・超硬やセラミックなどの非常に硬い素材の加工には向いていません。
・ビビリの抑制や加工精度を保証するため、高剛性の加工機や周辺環境による共振の対策が必要です。